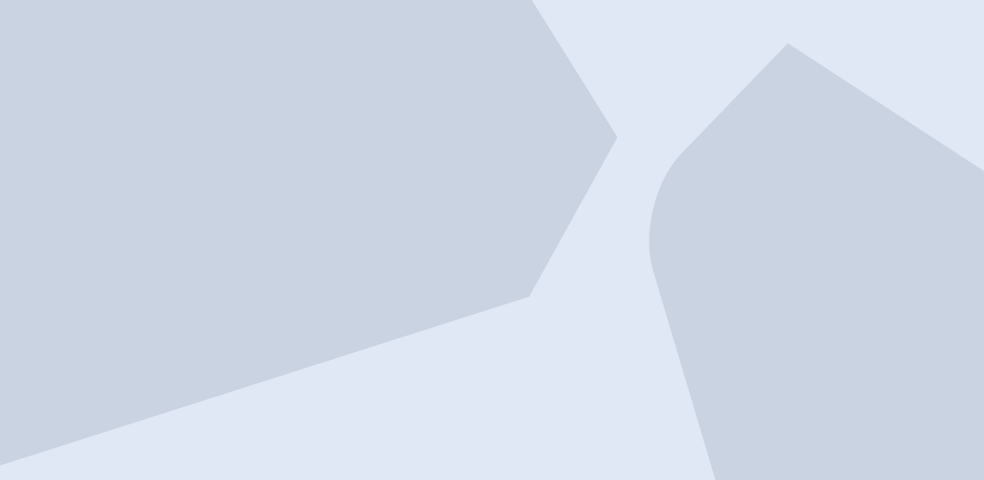
Joerg Muenzing
Fähigkeiten und Kenntnisse
Werdegang
Berufserfahrung von Joerg Muenzing
Operations Consultancy, turning underperforming operations into high performing assets, while creating a competitive advantage from superior quality, speed, efficiency. With core competencies in industrialization, rationalization, and turnaround management, the company helps executives and investors in solving operational constraints, streamlining processes, and driving mission-critical projects to success.
Managed global Quality Excellence initiatives, enhancing satisfaction and cutting losses. Led Agile Engineering, doubling successful product launches. Implemented Quality Excellence, reducing Tunisian plant defects by eight-fold. Spearheaded Operations Diagnostics, boosting efficiency and quality, while pioneering Digital Transformation, Factory of Future, and Lean Production System concepts. Conducted global benchmarking to strengthen safety technology leadership.
- 1 Jahr und 1 Monat, Juli 2022 - Juli 2023
Strategic Advisor
NEOM
Spearheaded a Supplier Development program in the Industrial Design and Construction (ID&C) sector, systematically assessing and certifying offsite manufacturers and onsite contractors for the construction of a futuristic mega city NEOM. While leading its development and execution, introduced a pioneering Global Certification Standard, published as a handbook, aimed at revolutionizing the construction industry.
Developed a Factory Efficiency program to debottleneck the main antidiabetic drug plant for the U.S. market in Mexico. Targeted improvements reduce downtime by 33%, doubling throughput to €2.5 billion without capital investment through massively increased equipment effectiveness (OEE). Program is currently underway. “The seed of improvement is now in our minds” – Operations Director.
- 1 Jahr, Jan. 2022 - Dez. 2022
Operations Turnaround Strategist
LEO Pharma
Guided a Factory Turnaround program with a focus on boosting operational efficiency (OEE) by addressing flow constraints, process deviations, and compliance issues, under the scrutiny of the French labor unions. In just 12 months, efficiency doubled, achieving a 32% throughput increase without capital investment. Stock-outs and backlog were eliminated, process deviations decreased by 25%, and lead times reduced from 140 days to under 80 days.
- 8 Monate, Nov. 2020 - Juni 2021
Quality Excellence Architect
FormFactor
Initiated a Quality Excellence program to reduce non-quality costs (NQC) and improve customer satisfaction through systematic root-cause elimination for equipment dead-on arrival (DOA) and defects-per-unit (DPU). Responsible for developing the program, establishing a zero-defect mindset, coaching cross-functional teams in USA and Germany to improve product maturity and process capability that bring defect rates and costs down to target levels.
Guided the Strategy Development initiative to chart a five-year vision for Operations. This involved designing the future-state and target operating model (TOM), assigning executive authority, responsibility, and accountability (ARA), and developing a strategy deployment roadmap to achieve breakthrough objectives. Furthermore, served as speaker at the group’s performance conference: “How to Systematically Boost Performance Without Capital Investments, Endless Meetings, and Complex Processes.”
Led Lean Transformation program for factories in Sweden, Denmark, and France, driving them toward world-class manufacturing (WCM). Oversaw diagnostics, program development, performance reviews, shop floor engagement, and skill development. Introduced 'World-Class Manufacturing Summit' leadership training and Operational Excellence program, yielding annual scrap reductions of 8%, unproductive time reductions of 28%, and productivity increase of 9%.
Revitalized and expedited an underperforming Cost Reduction program, strategically focusing on cost-per-move (CPM) by implementing adaptive maintenance, systematic problem analysis, and rigorous root-cause elimination. The collective effort resulted in the execution of over 300 projects, delivering $118 million in cost savings, run rate.
Spearheaded a Lean Transformation program to reduce operating costs in manufacturing and the supply chain, closing a profitability gap. Led teams across 20 production sites in various countries, resulting in 400 improvement projects that added CHF 36 million to the bottom line within 36 months. Trained managers and engineers in Operation Excellence and spearheaded additional initiatives to enhance first-pass quality, benchmark factory performance, and drive improvement through Lean Six Sigma Black Belts.
Developed an R&D acceleration program based on Agile principles to shorten time to market by 35% within 18 months, while streamlining the engineering-operations interface. After just 32 support days, R&D project delivery performance increased by 2.5x within the first seven months.
- 2 Jahre und 4 Monate, März 2016 - Juni 2018
Lean Transformation Leader
Norican | Disa & Wheelabrator
Developed the group's value creation program to increase speed and efficiency of focus factories and engineering centers. The pilot site in Denmark matured at 75% of world-class rate, improved schedule adherence from 33% to 82%, cut rework and overtime cut in half, while increasing productivity by 20%. In parallel, coaching the senior team in strategy deployment (Hoshin Kanri) to deliver on breakthrough objectives.
- 7 Jahre und 7 Monate, Juli 2010 - Jan. 2018
Lean Transformation Leader
Norsk Gjenvinning
Developed the industrialization program for Norway's leading recycling company. Within 18 months, transformed a poorly performing site from noncompliant to internal benchmark, resulting in 82% lower inventory and 31% higher labor productivity. Ongoing engagement to design new factories (Greenfield) and to drive performance improvements in the six largest plants, while building the skills and systems to sustain them.
- 2 Jahre und 1 Monat, Dez. 2009 - Dez. 2011
Global Head of Lean and Quality
Franke
Responsible for quality and factory rationalization to steadily raise productivity by +6% per year, while building the skills and capabilities to sustain them. A major plant in the UK, for example, improved productivity by 18%, reduced inventory by 37%, and shortened manufacturing lead-time from 10 to 3 days. After 18 months, critical processes were standardized, 300 managers certified in 28 Boot Camps, and nearly CHF 5 million improvements implemented.
- 1 Jahr, März 2009 - Feb. 2010
VP Quality EMEA, Task Force Leader
Landis Gyr
Led Quality Excellence to boost product reliability, reduce failures, and cut warranty costs. Formed 9 Quality Taskforce (QTF) teams, addressing hardware and software issues through FMEA and 8D frameworks. Established 'Quality Academy' for quality education. Led 60+ improvement programs across Europe, slashing warranty exposure by CHF 26 million and reducing field failures by 95% to 800pm. EMEA quality system served as APAC model, addressing defects and costs in other regions.
- 8 Monate, Apr. 2008 - Nov. 2008
Quality Turnaround Leader
Daimler, Detroit Diesel
Directed the Quality Excellence program pivotal in a turnaround effort, spearheading the Warranty Accrual Reduction (WAR) initiative. Managed the project team, achieving a $59 million reduction in warranty accruals within seven months. Enhanced diagnostics and repair efficiency through system improvements and process redesigns, preventing repeat failures. Recognized throughout the Group as a model for successful turnarounds.
- 3 Monate, Feb. 2008 - Apr. 2008
Lean Transformation Manager
Mercedes Benz
Led Factory Improvement program to recover delayed military vehicle production. Managed project and cross-functional teams, enhancing operations at assembly plant and integrating suppliers. Achieved 25% increase in assembly speed, 60% improvement in yield, and on-time delivery of all 82 vehicles in 10 weeks, resolving significant delay. Recognized by CEO Truck Division for impactful, tangible improvements.
- 1 Jahr, März 2007 - Feb. 2008
Operations Turnaround Manager
Navico (Lowrance, Simrad, B&G)
Hired in crisis for Manufacturing Turnaround, doubled throughput in Mexico, resolved bottlenecks in Norway and New Zealand. Achieved 44% labor reduction, 53% space savings, 94% inventory cut, 66% rework decrease, and $8M profit boost in 12 months. Over 7 years, productivity soared 1,100% with 31% CAGR, leading to acquisition. Engaged in strategic planning and complexity reduction from 2009 to 2020. CEO recommends for any manufacturing or supply chain role.
- 1 Jahr und 4 Monate, Dez. 2005 - März 2007
Factory Integration Manager
Techtronic Industries
Led a Factory Consolidation program merging two large assembly plants in Guangdong. Oversaw program development and onsite deployment, involving factory mapping, inventory analysis, budgeting, staffing, stakeholder alignment, and cross-functional leadership. Streamlined material flow and workload, right-sizing staff from 8,000 to 6,000. Achieved a 50% reduction in shortages and late deliveries, decreased on-hand inventories from 46 to 18 days, and added $20 million in manufacturing capacity to meet demand.
- 1 Jahr und 1 Monat, Feb. 2006 - Feb. 2007
Lean Transformation Leader
Gategourmet
Led performance improvement program to meet profitability targets, overseeing Lean Transformation across seven sites in Europe and Asia. Implemented cellular manufacturing, flow management, and daily scrum, achieving substantial productivity gains despite challenges including engagement with German unions. Resulted in annual savings exceeding CHF 5 million and closure of a significant European warehouse.
Ausbildung von Joerg Muenzing
- 1 Jahr und 7 Monate, Okt. 2000 - Apr. 2002
Business Administration
NSU Nova Southeastern University, Ft Lauderdale, USA
Graduated with honors, GPA 3.92.
- 4 Jahre und 10 Monate, Okt. 1989 - Juli 1994
Electrical Engineering
FHD Fachhochschule Darmstadt, Germany
Graduated among top 10%.
Sprachen
Deutsch
Muttersprache
Englisch
Fließend
Französisch
Grundlagen
XING – Das Jobs-Netzwerk
Über eine Million Jobs
Entdecke mit XING genau den Job, der wirklich zu Dir passt.
Persönliche Job-Angebote
Lass Dich finden von Arbeitgebern und über 20.000 Recruiter·innen.
22 Mio. Mitglieder
Knüpf neue Kontakte und erhalte Impulse für ein besseres Job-Leben.
Kostenlos profitieren
Schon als Basis-Mitglied kannst Du Deine Job-Suche deutlich optimieren.